Customer Success Story
AquaPhoenix Scientific
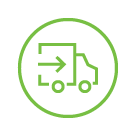
Industry
Manufacturing
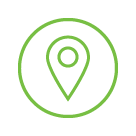
Location
Hanover, PA
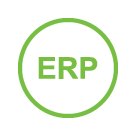
System Selected
Sage X3
Key Results
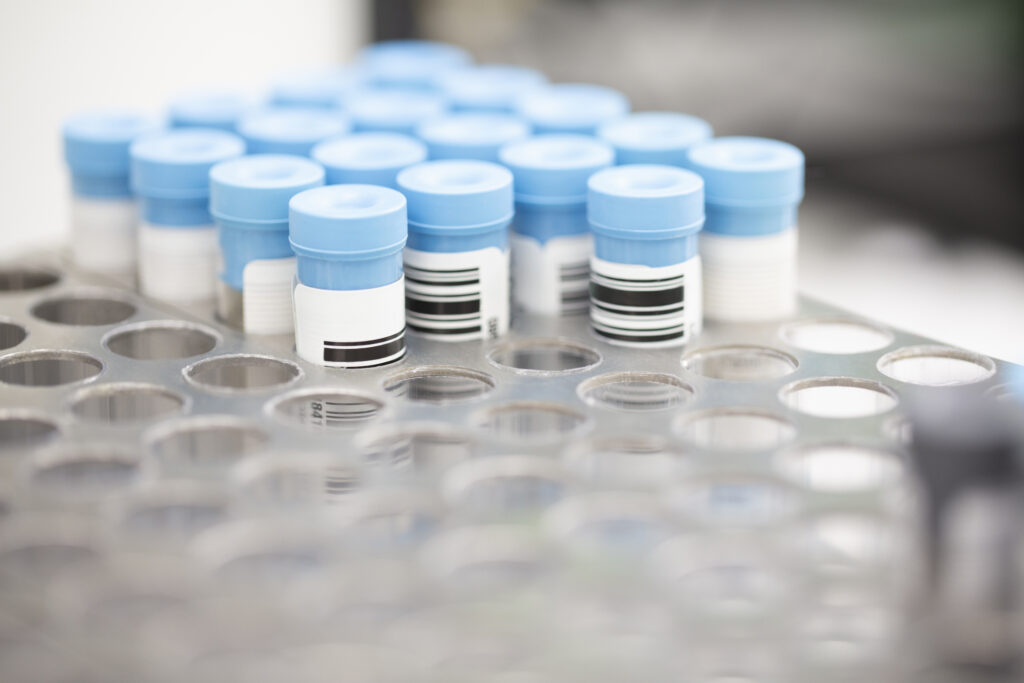
“We run a lean operation. We move fast, speak directly, and get things done. And we expect that same level of agility and results from our business partner and ERP application.”
Their Story
The company implemented Sage X3 15 years ago when its revenues were just $12 million. “Sage X3 replaced QuickBooks if you can believe it,” notes Medina. “We had completely outgrown QuickBooks, to put it mildly.”
Medina recalls that AquaPhoenix reviewed several ERP applications (and even began implementing one) before deciding on Sage X3. “What we first saw in Sage X3 was its deep manufacturing capabilities and broad flexibility. Our owner is a visionary — he’s willing to take big risks for big
gains and saw the potential for Sage X3 to transform our operations.”
Partnership Passes the Test of Time
The company initially worked directly with Sage and then transferred to a local reseller. “They were good, but we were outgrowing them too,” recalls Medina. “We needed a partner with more product experience and manufacturing industry expertise. That’s when we engaged NexTec.”
A decade later, Medina says NexTec continues to bring value to the relationship. “As our business grows and evolves, we’ve customized Sage X3 to fit the way we work. NexTec handles those modifications for us, and they always use a best-practice approach that allows us to continue to take
advantage of Sage updates.”
Medina adds, “Another advantage NexTec brings is their network of connections and industry experience. They continually share what they’ve learned and what they see working with other companies. We’ve incorporated many of their suggestions in our operation.
Flexible, Scalable Workflows
Sage X3 powers workflows throughout AquaPhoenix, from supply chain to sales, with powerful capabilities that help the organization work faster, simpler, and with more flexibility.
For example, automatic journals in Sage X3 allow AquaPhoenix to control the accounting codes used to post transactions based on the type of transaction. The company can post to different sales accounts based on the customer or product — or to different inventory accounts based on the warehouse referenced in a product receipt. “This saves our finance team an incredible amount of time and gives us better, more granular reporting,” notes Medina.
The company also leverages the Sage X3 material requirements planning (MRP) functionality to make strategic purchasing decisions and reduce its inventory holdings. “The insight we get from Sage X3 MRP helps us optimize procurement and ensure we have the right products on hand at the right time,” Medina adds.
AquaPhoenix has automated workflows across every department, all with the goal of a leaner, greener, more profitable operation. “With Sage X3, we’ve effectively shaved hours off many processes,” says Medina. “And we’re continuing to expand how and where we use the software.”
A Culture of Continuous Improvement
AquaPhoenix continually looks for opportunities to reduce waste and improve efficiency through its lean manufacturing initiatives. As part of that quest, every aspect of the company is open to suggestions for improvement — in fact, the company actively solicits such suggestions from its employees.
“We encourage our people to look for improvements, and as part of that, we foster a culture of acceptable failure and rapid change. When the fear of making a mistake doesn’t constrain people, they can work more efficiently and creatively, fostering a continuous improvement culture. To achieve this, we need a business management solution that’s fast and flexible too.”
Dynamic Demand Planning
Sage X3 is an ideal fit for the company’s dynamic, fast-paced manufacturing scheduling workflow. While some manufacturers plan workloads for the coming weeks or months, AquaPhoenix does its planning in real time.
Within Sage X3, NexTec configured a dashboard that consolidates work order and sales order data to provide the company’s shop floor teams with up-to-the-minute information about upcoming production tasks. “Our goal is to ship every order by the following day,” explains Medina. “By getting the information into our teams’ hands more quickly, we reach that goal more often.”
Quality is the Driving Force
Quality is at the forefront of the company’s daily operations, and the commitment is reflected by its ISO 9001 certification. Sage X3 plays a significant part in achieving and maintaining this certification.
For example, the company uses the Sage X3 customer support module to track customer concerns. “Plus, we log all internal non-conformances in Sage X3, so we can quickly identify a quality issue,” Medina explains. “This allows us to identify areas of improvement and further drives our lean initiatives. Our teams meet weekly to review their area’s performance — and the data they’re reviewing and acting on comes from Sage X3.”
The company also uses the robust quality management functionality built into Sage X3 to track the test results its chemists run on its manufactured products. Sage X3 offers a fully integrated quality control process that allows AquaPhoenix to rigorously enforce inspections and ensure its products comply with internal and industry standards.
Best Technical Talent in the Industry
“I’ve worked with other vendors, including other Sage partners, but I believe NexTec Group has the best technical talent in the industry. We continually push Sage X3 to do more, and NexTec is right there with us to help make it happen.”