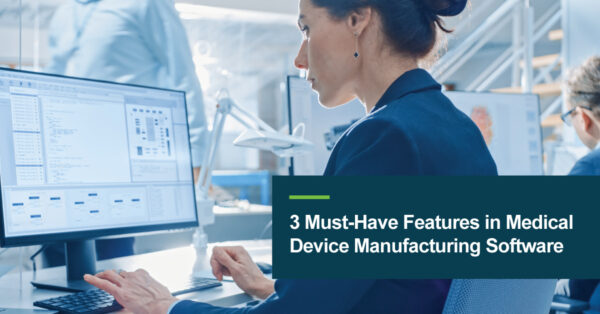
Right now, concerns about inflation and a looming recession plague most industries, but there’s one industry that doesn’t seem overly concerned. According to Nick Paul Taylor in a recent MedTech Dive article, the medical device industry is “confident it can ride out [a] recession.”
Even so, there are a few other challenges that pose a threat to the industry. Taylor writes: “Analysts at RBC Capital Markets are reassured that the medical device sector is equipped to weather an economic downturn as the industry’s latest earnings season comes to an end. However, medtech companies are still facing challenges like hospital staffing shortages and supply chain constraints that have been ongoing for several quarters.”
The industry’s ability to handle the current economic upheaval is good news, yet the financial pressure—as well as the labor and material shortages—can still negatively impact medical device manufacturers’ ability to serve their customers and their bottom line.
So what can they do to overcome these issues?
They can implement medical supplies software and medical devices software within a comprehensive Cloud ERP solution to increase their efficiency, productivity and profitability—but not just any medical device manufacturing software will do. The right medical device manufacturing software must include a few vital features, and we’ll reveal what these specific features are today.
The 3 Features Medical Device Software Must Have
Medical device and supplies software is software purpose-built to meet the needs of the medical industry. Data from every department—finances, sales, purchasing, production, customer management and more—flows into the Cloud ERP solution in real time, syncs with every application (including integrated third-party applications) and is shared with and accessible by every team member (with the proper permissions, of course). Business workflows and processes become streamlined and efficient while collaboration, compliance and security is managed within one, centralized system.
The benefits are clear, but the software must provide the following three features for it to be truly effective:
- Inventory and Distribution Management
- Keep track of inventory movement with advanced lot traceability functionality and Warehouse Management Solutions (WMS).
- Use updated inventory data to make accurate forecasts and better, faster business decisions.
- Manage and analyze production costs.
- Streamline purchase order workflow approval.
- Integrate sales order and fulfillment center warehouse to the ERP solution via API as well as integrate with other control systems.
- Manage global warehousing and logistic needs from one platform that provides a “single source of truth.”
- Gain real-time visibility into inventory quantities and cost.
- Production Order and Tracking
- Financial Management, Business Intelligence and Reporting Tools
Managing inventory and distribution processes is a complex undertaking. Resources used to create a final product must be tracked by serial and lot number as well as expiration date. If a medical device manufacturer has one or multiple warehouses, having accurate knowledge of what resources are available and where they’re located is almost impossible for manufacturers using aging technology or maintaining manual inventory counts with spreadsheets.
With the right ERP solution and industry-specific software, medical device manufacturers are able to automate their inventory and distribution management processes. They can:
And medical device and supplies software automates the inventory replenishment process, ensuring the correct materials and resources are on hand at all times.
Production orders provide the what, when and how of producing a material. From defining the material to be produced and where the production takes place to the required time to completion and how much has been ordered, production orders rely on accurate inventory data. To ensure success, manufacturers need real-time access to operational information and production data as well as lot-tracking, expiration dates and traceability capabilities—and they get it with medical device and supplies software. They also get Material Requirements Planning (MRP) and advanced scheduling, bill of material with full revision tracking and quality control capabilities.
Built-in business intelligence and reporting tools allow manufacturers to analyze company-wide data and present their insights in dashboards, visualizations, charts and graphs. They can also monitor personalized KPIs and review workforce efficiency from a centralized database.
Altogether, these three must-have features allow medical device manufacturers to increase their visibility and efficiency as they work to overcome unprecedented economic crises.
Finding the Three Must-Have Features in One Award-Winning Solution
Recognizing that a Cloud ERP solution with medical device manufacturing software as a necessary tool in today’s marketplace is incredibly important. But it’s just as important to determine which solution is best for a medical device manufacturer’s specific needs.
NexTec Group’s ERP Selection Guide: Medical Supplies and Devices suggests businesses start the process by setting up a review team, and with help from a consulting partner, identify areas that would benefit from a connected business management system. From there, compare ERP options.
NexTec recommends Acumatica Cloud ERP. From real-time collaboration, reporting and analytics to future-proof functionality, Acumatica’s cloud-based ERP solution, which also includes integrated inventory management software, warehousing management software and distribution software, has the industry-specific functionality, along with the ability to integrate with third-party applications, that medical supplies and devices companies need. In addition, because it’s based on mobile technology, every team member can access the solution from anywhere and at any time, using any web-enabled device of their choice.
To learn more about Acumatica Cloud ERP, contact the experts at NexTec Group. We’ve been advising companies on the best technology for over 28 years, and we’d love to chat.