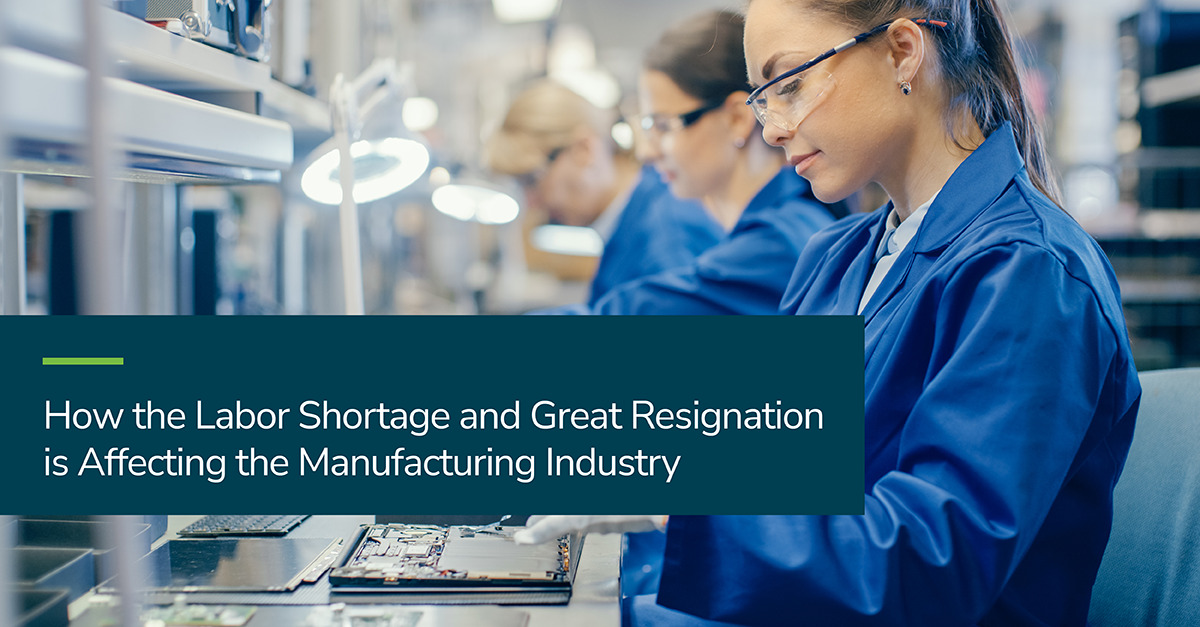
Most people have heard the term “The Great Resignation” and understand there is a concerning lack of labor available in every industry. But knowing the term and that there’s a problem is not the same as understanding what impact the mass exodus and the resulting critical labor shortage are having on individual industries, such as the manufacturing industry.
Today, we’ll look at what “The Great Resignation” is—and is not—as well as how the manufacturing industry can utilize manufacturing management software to overcome these ongoing challenges.
The Great Resignation: What is It?
“The Great Resignation” is a term coined by Anthony Klotz, an associate professor of management at UCL School of Management. The definition is that people are leaving their jobs in droves in response to the pandemic, with the US Bureau of Labor statistics showing over 47 million Americans quitting their jobs in 2021. But according to a recent DW article, “The Great Resignation” would be more accurately described as “a Great Reshuffle.” Author Nik Marin spoke with Klotz about his forecast of mass resignations, and it appears there was a misunderstanding of what he was predicting.
Klotz told Marin, “A lot of people heard me say everyone’s going to leave the job market, and that’s not what I was saying at all. I predicted an increase in resignations and it stands to reason that the vast majority of them were going into other jobs.”
In addition to Klotz’s belief that people were heading to “greener pastures” and not just staying home, a Harvard Business Review article says a quitting trend has been going on for years, with the average monthly quit rate increasing by 0.10 percentage points each year from 2009 to 2019. After the 2021 stimulus checks, there was a surge in workers quitting, adding to the overall labor shortage.
Whether “The Great Resignation” is a recent phenomenon or the continuation of an alarming trend, many companies have been left with a bare-bones workforce, forcing them to reimagine their workplace environment. In fact, workers are now demanding a more flexible working environment, an improved work-life balance and higher pay. And until recently, these workers have had the upper hand.
Unfortunately, the advent of inflation and recession along with the resulting layoffs by high-profile organizations (e.g., Facebook, Microsoft and Intel, to name a few) may portend another shift in employee-employer relations. Still, no matter how it plays out, one thing is certain: the ongoing labor shortage is severely affecting the manufacturing industry.
The Great Resignation: How the Manufacturing Industry Has Been Impacted
According to a Manufacturing Tomorrow article, the manufacturing industry has been hard hit by “The Great Resignation.” The article notes, “Quit rates in the sector [manufacturing] were 58% higher in 2021 than pre-pandemic levels, almost 20% more than the second-highest change. While employment in the industry has slowly declined over the years, losses this significant are historic.” A few of the side effects of losing so many workers include factories struggling to meet demand and losing those employees who stayed due to them being “overworked and stressed.”
An article by the American Society of Mechanical Engineers (ASME) also reflects on the manufacturing industry’s labor concerns. Authors Steven R. Schmid and Shreyes N. Melkote write that the labor shortage is a long-term trend that has been “exacerbated by pandemic effects.” They lay out multiple reasons why there’s a skilled labor shortage:
- Workers displaced by the pandemic-related closures changed jobs/careers.
- Better paying jobs or work environments enticed some workers.
- Highly skilled professionals have embraced entrepreneurship.
- More automation has displaced assembly worker positions with robot setup and programming technician positions.
- A “silver tsunami” of retirements by the Baby Boomer generation.
The authors note, “It has been estimated that, even after increased recruitment of new employees, a shortfall in excess of 2 million skilled workers will exist in the American manufacturing sector, and over 300,000 too few engineers.”
The Great Resignation: How Manufacturing ERP Software Can Help
With the manufacturing industry in a challenging position, manufacturers are desperately seeking ways to entice workers while simultaneously cutting costs. The good news is that modern manufacturing management software can help them do both.
With modern manufacturing management software within a comprehensive Enterprise Resource Planning (ERP) solution, manufacturers have a single system that supports and automates business processes, which helps create efficiencies not possible with disconnected systems and manual interventions. ERP software also acts as the centralized database for departmental data. In the face of debilitating labor shortages, manufacturing Cloud ERP software can help streamline workflows, automate business processes and integrate with crucial third-party applications, which allows manufacturers to increase productivity and reduce costs.
For Industrial Specialty Services (ISS), a company that provides integrated mechanical services and solutions to the refining, petrochemical, gas, power, pulp & paper, offshore, and subsea markets, a modern ERP system was exactly what they needed. ISS was established in 2020, and from the get-go, CEO James Craig knew that Acumatica Cloud ERP was going to be the technology platform on which he would establish his newly formed company.
“The primary idea was to create a solution that was designed around the cloud,” says Craig. “It was a critical element because we wanted to get away from maintaining servers or being responsible for them.”
Industrial Specialty Services (ISS) CEO, James Craig
He adds, “We needed a solution we could trust and that we knew would work with the services we provide.”
With the help of two strategic partners, which included NexTec CEO Eric Frank, Craig and his team were able to implement Acumatica in six months while facing a number of challenges, including a global oil price drop, the pandemic, and three hurricanes. Since then, they’ve enjoyed a flexible, scalable, and centralized ERP and collaboration platform that provides unmatched control and visibility, the ability to access data in real time, and an intuitive and user-friendly interface.
Because Acumatica doesn’t charge for the number of users but for the resources consumed, ISS has avoided additional user-fee costs. Craig says, “As far as back office goes, we can absorb a majority of employees and only need maybe two people in admin roles to handle safety requirements.”
With such an effective and affordable ERP system in place, ISS is able to manage their business processes with fewer people by automating labor-intensive activities (e.g., reporting and improving workflows), and if—or when—they need and are able to find qualified workers to add to their team, they can do so without paying for additional user licenses. Additionally, the cloud-based voice, data, and business application services eliminates the need to invest in a large IT department, lowering their overall salaries and wages.
Finally, by utilizing data from every department through the ERP system, the ISS team can see how the organization is operating, if there are any bottlenecks that need to be resolved, what resources are needed (and when), if employees are prioritizing jobs and more, increasing efficiency even in the face of labor shortages.
The Great Resignation: Let Acumatica and NexTec Help
Ultimately, “The Great Resignation” (or the “Great Reshuffle”) will continue to challenge manufacturers for the near future. As such, they should evaluate Acumatica’s manufacturing ERP software based on what it can do to help them manage their production, estimating, engineering, material planning, scheduling, and production configuration needs (as well as their document management, CRM, project accounting requirements) within a single, integrated system.
By having the right system in place, manufacturers can give their existing employees a sophisticated tool that will help them manage their complex processes. And as the manufacturers add team members, they’ll be able to train them quickly and easily on an intuitive, user-friendly solution.
At NexTec, we help manufacturers through the implementation process and offer exceptional support once they’re live. With over 28 years of experience in advising and assisting companies on choosing and implementing the best technology, we’re confident that Acumatica manufacturing can help every manufacturer through this difficult time and ensure their success in today’s digital economy.
For any questions or to set up a demonstration, contact us today. We’d love to chat.