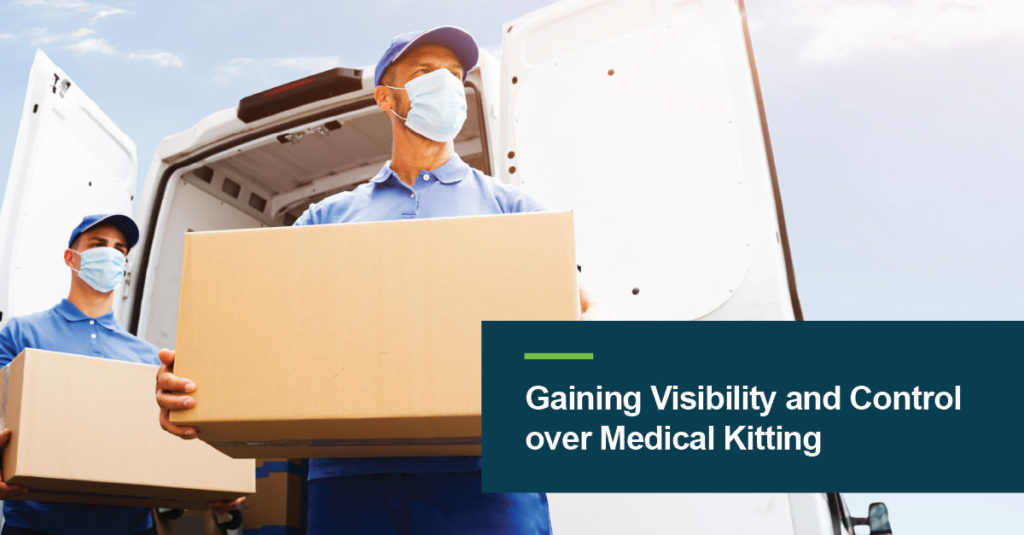
Medical kitting is a popular practice in the medical supply and device industry, and when done efficiently, profits can increase. For medical supply and device manufacturers and distributors, the best way to manage the medical kitting process is with medical supplies software and medical devices software embedded within a Cloud ERP solution.
Let’s examine what medical kitting is, how medical supplies and devices ERP software helps with the kitting process and how one company used ERP software to gain visibility and control over their medical kitting operations.
What Medical Kitting Is
Simply put, medical kitting is the practice of packing individual medical supplies or devices (or both) into one kit for hospitals, surgery centers and healthcare facilities, as well as for people at home. A kit can include any number of items, such as surgical tools, instruction sheets and accessories.
Easy to describe, yet medical kitting is not easy to do. There are many before, during and after steps that need to be taken while assembling a kit, making it a complex and exacting process.
For example, companies need to track each component within a kit as well as track the kit itself. Medical supplies and devices companies operate under strict regulatory requirements, including having sterile storage facilities and complying with Current Good Manufacturing Practice (CGMP) regulations for the handling and distribution of finished pharmaceutical products, which means their inventory and fulfillment protocols must be on point. Shipping must be accurate and fast. And should a recall occur, medical supplies and devices companies must know everything about their products, from where they are and who has them to when their customers received them and how to inform the customers of the recall.
With such high expectations, it is essential for companies within the medical supply and device industry to invest in a modern business management solution, like Acumatica Cloud ERP. That’s exactly what InBios International did—with phenomenal results.
Medical Kitting (and More) with Acumatica Cloud ERP
InBios specializes in the design, development and manufacturing of immunodiagnostic devices for infectious diseases and biothreats. The company also provides assembled kits for its customers. Before Acumatica, InBios was relying on in-house software for their sales, inventory and medical devices management.
Says Manufacturing Manager Bryan Deszell in the company’s customer story, “We were running more than half the business with spreadsheets and email. Without accurate, current inventory numbers, we couldn’t keep up with growing demand. We simply weren’t confident in what we had on hand and what we needed to order. We needed to scale the business, and that required that we move to an ERP solution.”
NexTec Group helped the InBios team get Acumatica’s distribution software and inventory management software up and running. NexTec also built several customizations for their unique workflows. As a result, the company is more efficient, streamlined and effective.
They now have:
- Improved inventory control throughout the supply chain: “It had become nearly impossible to determine if we had enough components to fulfill our orders. Sometimes we’d have five people counting what was on the shelves and matching them to orders to see if we had enough. Now we have that information available in real time,” Deszell says. “[With Acumatica,] we’re able to connect purchase orders to production orders through to sales orders. We trust our numbers. That’s something we didn’t have before.”
- Increased traceability: “We can now track lot numbers within the system with forward and backward traceability. Before lot tracking involved too much time, too much paper, and lots of manual tasks.”
- Improved forecasting accuracy: “Previously we did hand counts frequently to determine exactly what we had on hand and what we needed to order. Now, the software can analyze prior years’ sales to help us identify seasonal trends for our products.”
They also manage their medical kitting more economically by ordering their raw materials in “optimal quantities at the ideal time,” which “saves money in carrying costs.” Deszell says, “We’re now better able to meet demand, with much less time spent—and much less stress.”
Additionally, the company has streamlined their FDA compliance reporting. They no longer store their compliance data using a whole floor of their building. Instead, they have everything they need in Acumatica’s comprehensive and connected solution.
“I can see us growing another 10-fold or more without outgrowing Acumatica,” Deszell says. “It’s the core of our manufacturing operations and the platform we’re building the business around.”
Gain Visibility and Control Over the Kitting Process
Every medical supply and device manufacturer and distributor can gain visibility and control over their medical kitting process by implementing Acumatica Cloud ERP. The cloud-based solution provides users with insights into the order, inventory, purchasing, customer relationship, business and financial management aspects of the operation. With this single solution, users can track orders and lots (with automated serial tracking), manage inventory, access critical data at any time via any web-enabled device and seamlessly integrate with critical third-party applications.
To learn more, download our free guide, Why Distribution and Inventory Management are Critical for Medical Supplies and Devices Companies. And contact our team today. We’d love to chat.